The Cupid Series Precision Laser Cleaning Machine is a versatile and efficient tool designed for a wide range of cleaning applications, from automotive maintenance to aerospace parts cleaning. With its large laser spot, high single pulse energy fiber laser, and multiple safety features, this machine offers a reliable and safe solution for various surfaces. However, even the best machines can encounter issues. Below, we outline common troubleshooting steps to help you resolve potential problems with your Cupid Series Precision Laser Cleaning Machine.
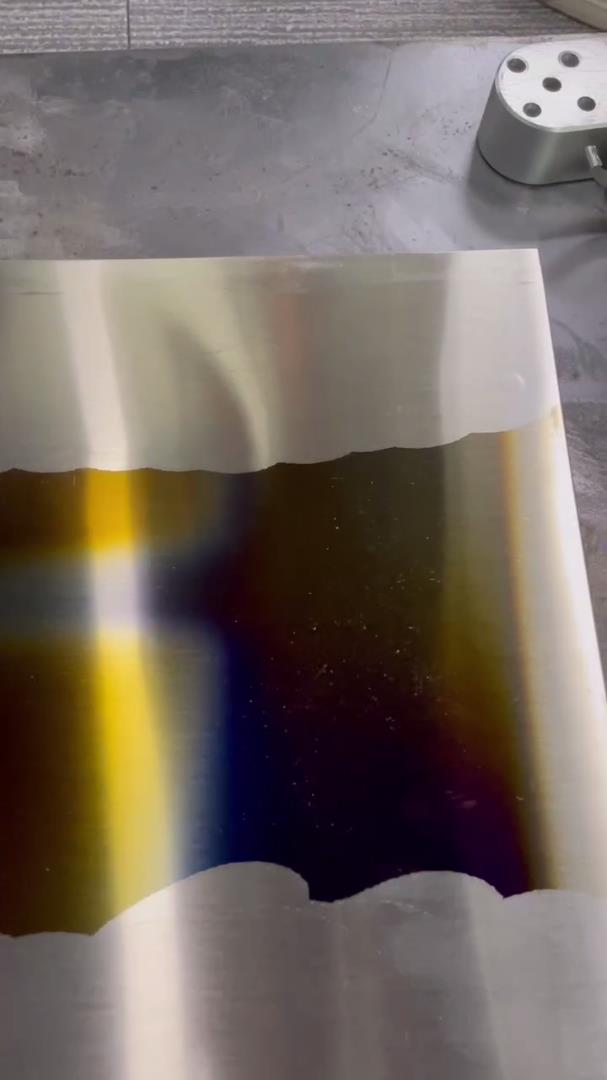
1. Laser Not Firing
Possible Causes: – Power supply issue. – Emergency stop (E-Stop) button engaged. – Laser safety door not properly closed.
Troubleshooting Steps: 1. Check Power Supply: Ensure the machine is plugged into a working outlet and that the power switch is turned on. 2. Reset E-Stop Button: Locate the E-Stop button on the high-speed cleaning head and press it to reset. 3. Verify Safety Door: Ensure the laser safety door is fully closed and latched.
2. Inconsistent Cleaning Results
Possible Causes: – Incorrect working parameters. – Lens contamination or damage. – Inadequate shielding gas supply.
Troubleshooting Steps: 1. Review Parameters: Check and adjust the working parameters stored in the machine to match the material and cleaning requirements. 2. Inspect Lens: Clean or replace the lens if it is dirty or damaged. Remember, almost all electrical parts, including lenses, are from imported brands and can be replaced easily. 3. Check Shielding Gas: Ensure the shielding gas function is activated and the gas supply is adequate.
3. Machine Alarm and Shutdown
Possible Causes: – Overheating. – Sensor malfunction. – Safety circuit trip.
Troubleshooting Steps: 1. Check for Overheating: Allow the machine to cool down and ensure proper ventilation. 2. Inspect Sensors: Check all sensors for obstructions or damage and clean them if necessary. 3. Reset Safety Circuit: If the machine has shut down due to a safety circuit trip, locate the reset button (usually near the main power switch) and reset it. Note that the Cupid Series features European standard safety circuit design to prevent sudden power-offs.
4. External Control Failure
Possible Causes: – Connectivity issues. – Incorrect parameter settings. – Faulty external control device.
Troubleshooting Steps: 1. Check Connections: Ensure all cables and connectors between the machine and external control device are properly seated and not damaged. 2. Verify Parameters: Confirm that the parameters called by the external device match those programmed in the machine. 3. Test External Device: Use a known good external control device to test the machine’s external control functionality.
5. Lens Service Life Reduction
Possible Causes: – Inadequate shielding gas. – Frequent exposure to contaminants. – Incorrect cleaning patterns.
Troubleshooting Steps: 1. Optimize Shielding Gas Use: Ensure the shielding gas function is always enabled during cleaning to protect the lens. 2. Regular Maintenance: Clean the lens regularly and replace it if necessary to maintain optimal performance. 3. Adjust Cleaning Patterns: Use easier clean modes and more efficient cleaning patterns to reduce lens wear.
Conclusion
The Cupid Series Precision Laser Cleaning Machine is a powerful tool for a variety of cleaning applications, but like any advanced machinery, it can occasionally encounter issues. By following the troubleshooting steps outlined above, you can quickly resolve common problems and ensure that your machine continues to operate efficiently and safely. Remember to always refer to the machine’s manual for additional guidance and contact the manufacturer’s support team if you encounter any unresolved issues.
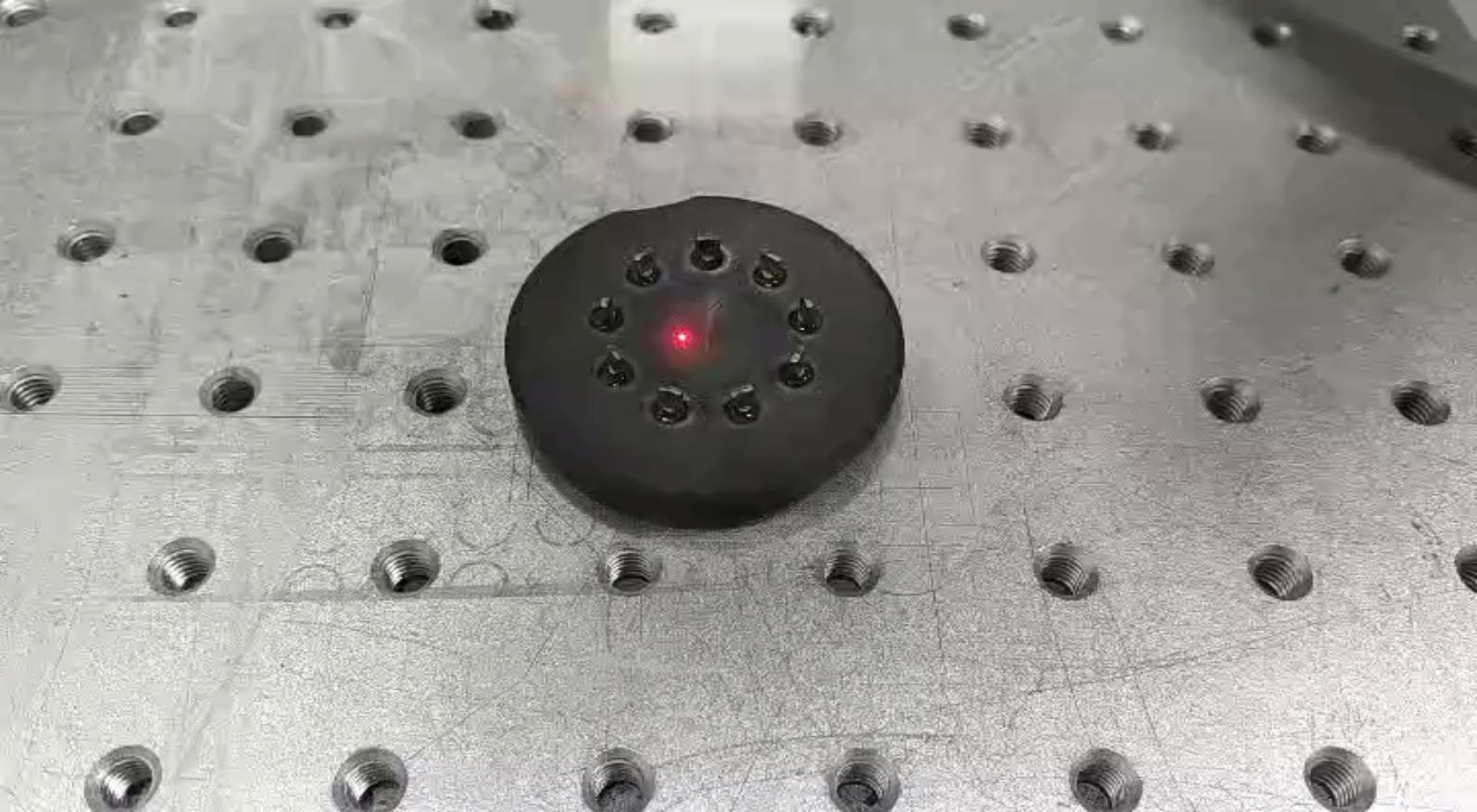